How can we help you?
From the Loudspeaker Diaphragm
- November 02, 2017
- Comparisons Loudspeakers
Like any engineering venture, the choice of material for a loudspeaker diaphragm, also referred to as a cone due to its typical contour, comes with a set of trade-offs that will impact performance. Often, the benefit of a given material for one performance goal poses a setback for another purpose – or purposes.
Even for a single purpose, say a smooth frequency response, we have to live with compromises that differ from material to material. Ideally, a diaphragm should be able to reproduce all frequencies in the audible spectrum at exactly the same intensity – a rather tall order! To look at what this entails, we need to consider how the diaphragm does its job. Basically, the voice coil interacts with the magnet to move like a piston in sync with the electrical signal that drives the loudspeaker. The diaphragm, on the end of this piston, pushes and pulls air in front of it to transmit sound into the space in front of it. To meet our design objective, our diaphragm should be as light, stiff, flat, and cost effective as possible. And that’s just ONE design objective! Aerospace engineers coined a term for this kind of ideal material – unobtainium.
Still, there are choices we can make to maximize performance for a given application. Historically, the most common choice for a diaphragm is paper. A well engineered paper is often stiff enough and light enough to meet the needs of a multitude of applications. Voice reproduction is often accomplished with a simple paper cone, which can be corrugated around the outer circumference to help suspend the diaphragm in the loudspeaker frame, or basket. Now, in a loudspeaker, paper is not your simple stationery variety. A number of different fibers are often added to the pulp in the manufacturing process to adjust the performance characteristics such as stiffness, damping, and elasticity.
Increasingly, environmental concerns are driving the choice of diaphragm materials. One of the challenges with paper diaphragms is the absorption of airborne moisture. The added mass can affect the speaker performance characteristics. Luckily, other cone materials such as mylar or polypropylene can be used cost-effectively to meet the needs of applications in these harsher loudspeaker environments. On the opposite end of the spectrum, in very dry environments, electrostatic interference with the speaker’s driving circuitry can be a challenge met with the appropriate choice of cone material.
Have questions? Let us help. We are your source for audio solutions.
Email: contact@Stetron.com
Customer Service: Canada: 1-877-716-0751 U.S.A: 1-800-925-3002.
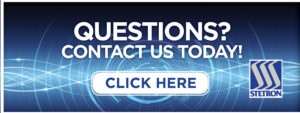